If you are in need of fully assembled printed circuit boards (PCBs) for your products, but you don’t know where to start, this article will guide you in the right direction. If you don’t have any printed circuit boards or any of the parts, and you certainly don’t want to burden your limited staff with the task of putting all those PCBs together, you will need a full-service PCB assembly provider.
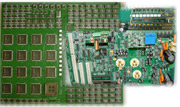
ACME PCB Assembly is an ISO 9001:2015 certified EMS. We make sure you get best price with highest quality, on time delivery schedule. All PCBs are meet the high standards established by the IPC 600. Since ACME PCB Assembly is a IPC certified trainer for IPC A-610, we know how important the quality of bare board is, and we know what can drive the PCB Assembly labor higher.
Being a full-service PCB assembly provider means that we handle every aspect of the project. You just give us your specs, and we’ll do everything else, including:
- Fabricating the printed circuit boards
- Ordering all the components of the PCBs
- Assembling the PCBs according to your specs
At Acme PCB Assembly, we have the experience, the vendor relationships, and the well-trained staff of fulfill your PCB order. The great thing about full-service PCB assembly is that you don’t have to worry about a thing. You don’t have to find the right parts vendors or ship materials to us. We handle everything.
We closely match new incoming inquiries to board house equipment and capabilities, ensuring you receive only those inquiries that you are interested in Acme Circuit board assembly provide PCB fabrication service in the development and manufacturing of quality single, double sided and Multi-Layers printed circuit boards for the computer, medical, transportation, communication, aircraft, aerospace and related industries.
Of course, if you already have printed circuit boards on hand and the PCB components you need, then you can also opt for partial service.
Contact us today to learn about all of our service options, including our add-on services.